advintec TCP - Calculation and calibration of robotic tools and fixtures in up to 6 dimensions
The challenge
Continually securing the correct operating position for fixtures and robotic tools such as welding torches and milling tools.
The solution
The advintec TCP tool calibration system calibrates the tool or fixture electronically in up to six dimensions. It automatically corrects the robot program by the measured variations and ensures that the tool always operates at the correct position. advintec TCP is a high-precision calibration system that can be used for all robot types and most robotic tools, making it independent of specific manufacturers.
Your benefit
Correction takes place directly and automatically in the ongoing production process.
Sizes & dimensions
advintec TCP precision infrared sensors - available in three sizes (internal dimensions):
- 120 mm × 120 mm
- 240 mm × 240 mm
- 320 mm circular
advintec TCP high precision laser sensors - available in two sizes (internal dimensions):
- 120 mm x 120 mm
- 320 mm circular
advintec TCP XS sensor only available in 120 mm x 120 mm infrared
Calibration of robotic tools with advintec TCP - advantages
- Automatic absolute calculation of robotic tools and fixtures
- Auto-commissioning and ease of use
- Simplified Integration in the production line due to small footprint
- Robust sensor available in two sizes
- Multi-sensor-system (connection of additional sensors possible)
- Reduction of costs
- Prevents the production of defective parts
- Reduces scrap and rework
- Short setup times
- Automatic correction of the trajectory due to wear and tear or tool-replacement
- 100 % quality assurance
- Connection of the calibration system to the robot controller, i.e. the calibration procedure takes place in an evaluation unit and transfers correction values to the robot controller
- High process reliability
- No additional PC‘s required
- Logging of calibration data
- Data evaluation possible at all times
Technical data
Sensor type | 2 channel infrared 880 nm, pulsed at 2kHz |
Interface | Serial or field bus (DeviceNet, Profibus, Profinet, etc.) |
Calibration accuracy | 0.02 mm |
Typical calibration time * | 3 sec. complete 2D calibration 6 sec. complete 3D calibration 9 sec. complete 5D calibration 15 sec. complete 6D calibration |
Protection class | IP67 |
Dirty surroundings | Yes |
Casing | Aluminium |
Dimensions | 2 or 3 translations 5 (3 translations + 2 rotations) 6 (3 translations + 3 rotations) |
Automatic correction of tool data | Yes |
Fields of application | Arc welding, stud welding, spot welding, laser cutting, tig welding, glueing, milling, drilling, grinding etc. 6D: Gripper calibration, fixture calibration, power train applications, high precision applications |
CE mark | Yes |
Operating voltage | 10–34 V DC |
Connections | IBS connector, 5-pin, PE advance conn. |
* calibration times can vary depending on conditions
Integration of advintec TCP-3D in the production process
- Uncomplicated
- Reduction of robot programming to a minimum
- Speedy installation
- Easy set-up
- Logging of calibration-data: regular data evaluation possible at any time
- No additional PCs required
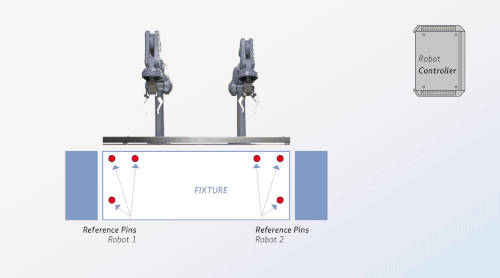
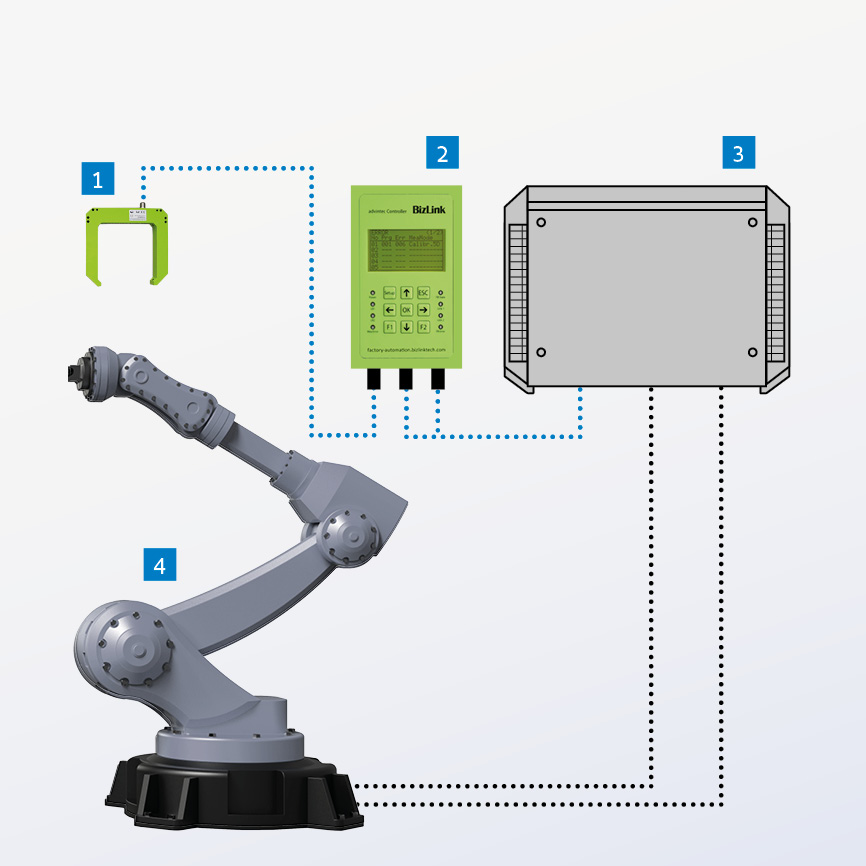
Integration of advintec TCP-3D in a robotic welding cell
Scope of supply of advintec TCP - calibration of robotic tools
- 1) TCP sensor
- 2) TCP controller
- Cable set (5 m): power cable, sensor cable, bus cable set
- Robot program examples
- Documentation download
Not included:
3) Robot controller, 4) Robot
Applications
Applicable for all rotation-symmetric tools
For special applications we offer you optional technology packages
TCP software milling
This software add-on was developed specifically for milling applications and allows the calibration of rotating tools with cutting edges such as milling tools and drill bits. In addition to the tool calibration it also contains a tool breakage detection.
TCP software stud welding
This software add-on was developed specifically for the calibration of stud welding tools with a foot. It facilitates the calibration of the stud or chuck, whereas the software can differentiate between the chuck and the foot.
TCP software sealant nozzle (hook nozzle)
This software add-on was developed specifically for the calibration of sealant nozzles with special geometries (hook nozzles) for hem sealing.
TCP software tandem torch
Both welding wires can be calibrated simultaneously.
TCP software cutting tools/blades
Enables a 6D calibration of cutting blades such as deburring knives and ultrasonic knives. Exact calibration of the cutting direction.
Mobile calibration case
To avoid time-consuming program modifications during plant extension or new tool setup work, we offer absolute initial calibration as part of an automated process. This keeps followup teach-ins to a minimum. The process involves the tool being moved to the centre of the photoelectric barrier, so as to generate the tool data. Only the tolerance zone (in which the tool is permitted to move) and the starting point of the calibration need to be taught-in to the system. Once complete, the robot moves the tool within the defined tolerance zone and calibrates itself automatically with the aid of the supplied program. The advantages here include the high level of precision and the automated, standardised and reproducible procedure, which is able to eliminate the kinds of human errors that occur with conventional manual calibration. In addition, initial calibration is also both rapid and cost-effective.
Get in touch with to get in touch for advintec TCP - calibration of robotic tools and fixtures!
Mobile calibration case for the initial calibration of unknown tools and fixtures (TCP & Base)
Flexible, mobile calibration for unknown tools and fixtures is now also possible with our mobile calibration case. Ideal for use when setting up new production lines.
Calibration case contents:
- Precision laser sensor 120 mm x 120 mm
- Infrared sensor 240 mm x 240 mm
- TCP controller
- Cable set
- Power supply unit
- Tripod for secure placement of the mobile sensors
- Data interface to robot control
- Software package
- Commissioning documentation
User login
Enter your username and password here in order to log in on the website
Publication